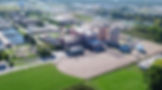
Green Bay, Wisconsin
Waste Water Treatment
Controls and Switchgear
This Waste Water project was part of a $169M investment by New Water to construct new biosolids treatment facilities within the Green Bay Waste Water Treatment Facility in Wisconsin. The facility, which was built in the 1970s treats domestic waste in addition to paper mill waste. The new biosolids treatment facilities included New digestion, reciprocating engine electrical power generation, dewatering and incineration processes, and implementation of nutrient removal and recovery processes. Enercon’s scope of supply for this project was providing the Switchgear and controls for the New Cogeneration and Emergency Standby Plant which included (2) dual-fuel blended digester and natural gas generator sets and (2) diesel standby generators.
How do our custom controls operate?
(2) CG170-20 anaerobic digestion Caterpillar Engines that are employing the Tem Evo Control.
Fuel blending between Natural and Bio Gas in 3 modes of operation with multiple utilities feeds, including black start operation.
Control of heat recovery valves: Jacket Water, exhaust, and aftercooler
(2) G3516C diesel Caterpillar Engines for both grid relief to the local utility and emergency backup power. The diesel and the gas generators are completely integrated.
The modernization of power equipment.
Enercon upgraded the diesel generator, switchgear, and controls; all originally commissioned in 2009. The project included the following components:
Woodward EasyGen controllers with CAN-to-fiber communication link to controllers in digester building
Updated engine controls for the (2) existing Caterpillar 3516C with unit mount EMCP 3.3 controllers
Schweitzer SEL-700G protective relays with PT/CT test blocks
Allen-Bradley 1756 ControlLogix PLC racks with EN2TR modules connected to plant Ethernet ring
Protocol converter/Gateway device for mapping all updated metering and alarm data
Integration of new start/stop logic as part of updated plant Sequence of Operations
Control and status upgraded and available to overall plant SCADA scheme
Main cogeneration control panels
The main cogeneration control panel utilizes an Allen-Bradley Plant Automation Controller and includes control logic for monitoring and controlling the new cogeneration units, providing the blending algorithm for the digester and natural gas sources and heat recovery of new cogeneration units to supplement the plant heating system.
The control panels for the biogas generators utilize Woodward Easygen controllers and are configured to interface with the Caterpillar TEMEvo engine controllers for total engine control.
Allen-Bradley ControlLogix Plant Automation Controller platform programmed within PlantPAx including door mount Industrial PC
Complex PLC rack configuration to accommodate plant P&ID structure with Ethernet ring connected network
Control logic included provided blending algorithm of the digester and natural gas sources and Cogeneration heat recovery to supplement the plant heating system
Mains, Ties, and Bus Ties included with Woodward LS-5 circuit breaker controllers integrated to simplify all control modes of operation
Protocol converter/gateway devices are utilized to gather all automation data and communicate with the plant SCADA network over fiber link
CAN-to-fiber converters provided for interconnection between biogas generator building controllers and diesel generator building controllers
Individual cogeneration panels for the (2) Caterpillar CG170 biogas generators
Design interface to the Caterpillar TEM-Evo unit controls for total engine control alongside unit Woodward EasyGen controllers
Mounting/wiring of PLC drop I/O for serial connection to wall mount CPU unit
CAN-to-fiber converters for EasyGen communication to Master Control LS-5 network
SHARE THIS
Project Specifications
15KV Arc Flash Rated Switchgear Lineup
- Provided power envelope for the Main-Tie-Generator-Bus Tie-Generator-Bus Tie-Main configuration
- Siemens/Enercon joint design venture to provide Arc flash exhaust plenum routing to the building exterior
- Mains and Generator protection used Schweitzer Engineering Laboratories (SEL) protective relays
- Mains and Generator sources provided with Allen-Bradley PM 5000 digital multi-function metering Package